High-Volume T-Shirt Printing for Schools and Organizations
High-Volume T-Shirt Printing for Schools and Organizations
Blog Article
Checking out the Art of Screen Printing: A Comprehensive Guide to T-Shirt Printing Techniques
When you enter the globe of screen printing, you're entering a domain where imagination satisfies workmanship. It's not nearly slapping ink on material; it's a careful process that requires the right tools and strategies. As you discover different methods, you'll discover just how to produce eye-catching tee shirt styles that stick out. Yet what are the necessary components you require to grasp before you can absolutely make your mark?
The Essentials of Screen Printing: Comprehending the Refine
Display printing, commonly called serigraphy, is a flexible method that allows you to transfer styles onto different surfaces. To get started, you'll first need to develop a stencil, which serves as the foundation for your style. This entails applying a light-sensitive emulsion to a display and revealing it to light, where your artwork obstructs the light from solidifying the emulsion.
Once you've rinsed the unexposed areas, you'll have a stencil ready for printing. Next off, you put the screen on your picked surface, like material or paper. You then use ink in addition to the screen and utilize a squeegee to press the ink through the pattern onto the surface area below. After printing, you'll need to cure the ink to guarantee it adheres appropriately. Comprehending these standard steps sets the stage for creating vivid, enduring designs via the art of screen printing.
Necessary Devices and Materials for Display Printing
To begin with screen printing, you'll need some vital devices and products. From the right tools to the inks and emulsions that bring your designs to life, each component plays an important function. Let's explore what you need to prosper in this creative process.
Display Printing Equipment
While diving right into the world of screen printing, you'll find that having the right tools is essential for attaining top quality results. Beginning with a strong display printing framework, which holds the mesh that transfers ink onto your fabric. You'll likewise require a squeegee for pressing the ink via the mesh. A top quality direct exposure system is necessary for creating sharp layouts when revealing your displays. Do not forget a washout terminal for cleansing your displays after printing. In addition, protective equipment like masks and handwear covers is essential for your safety and security. Ultimately, spend in a dependable heat source, such as a warm press or conveyor dryer, to heal your prints efficiently. With these devices, you're well on your way to understanding screen printing!
Solutions and inks
Choosing the appropriate inks and emulsions is important for accomplishing vibrant and resilient prints. You'll want to pick inks based on your preferred surface and fabric kind. t-shirt printing. Plastisol inks are preferred for their simplicity of use and great opacity, while water-based inks offer a softer feel and are more eco-friendly
Solutions serve as a light-sensitive layer on your screens, crucial for creating sharp patterns. Ensure to pick a high-quality solution that matches your ink kind; some emulsions work much better with plastisol, while others are ideal for water-based inks. Proper treating is additionally vital; it guarantees the ink adheres well and stands up to washing. By spending in the right inks and emulsions, you'll elevate your screen printing video game considerably.
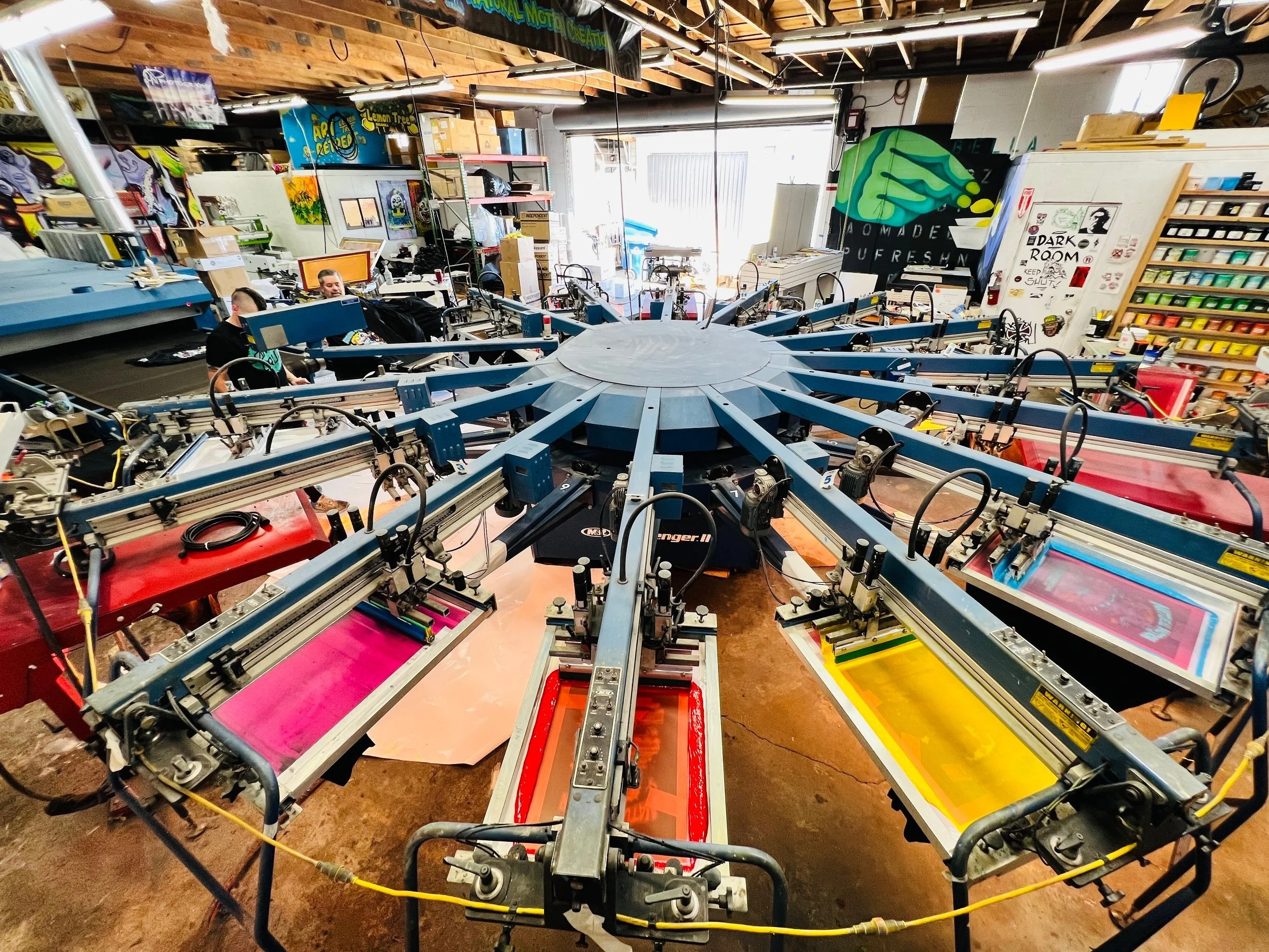
Devices for Application
You'll need a strong screen, preferably made of aluminum or wooden frames, along with a fine mesh for correct ink transfer. A squeegee is essential for using stress and spreading out ink evenly across the screen. With these devices, you'll be fully equipped for successful display printing!
Conventional Display Printing Techniques
Conventional screen printing methods have stood the examination of time, showcasing the art and workmanship behind this prominent method. You'll commonly begin with a pattern made from a great mesh material stretched over a framework. This mesh enables ink to travel through while blocking areas you want to remain unprinted. When you have actually prepared your design, you'll use a light-sensitive emulsion to the screen and subject it to a light, setting the solution where you desire ink to circulation.
After rinsing the unexposed solution, you're left with a pattern. You'll then place your screen on the t-shirt, use ink on top, and make use of a squeegee to press the ink with the mesh. This procedure can be duplicated for multiple shades, needing separate screens for every. The outcome? Dynamic, long lasting layouts that showcase your imagination. Mastering these methods gives you a solid foundation for all your screen printing ventures.
Modern Innovations in T-Shirt Printing
Today's tee printing landscape is buzzing with exciting innovations that are altering just how you produce styles. With innovations in digital printing, green materials, and advanced modification modern technologies, you can produce special, sustainable shirts like never ever previously. Let's check out these modern methods and see how they improve your printing experience.
Digital Printing Advancements
As digital printing modern technology has actually evolved, it's transformed the landscape of T-shirt publishing, providing you unmatched accuracy and imagination. Direct-to-garment (DTG) printing enables you to print directly onto textile, making it suitable for small runs or custom-made designs. With advancements in ink top quality, you can anticipate sturdiness and washability that matches display printing.
Eco-Friendly Materials Use
While exploring contemporary technologies in T-shirt publishing, you'll discover a growing focus on environment-friendly products that focus on sustainability without sacrificing high quality. Additionally, water-based inks are acquiring popularity, as they produce much less harmful runoff compared to standard solvent-based inks. These inks are not only much safer for the atmosphere but likewise supply lively colors and soft textures on fabric.

Customization Technologies Advancement
You now have access to digital printing techniques like Direct-to-Garment (DTG) and Dye-Sublimation, which permit for brilliant colors and intricate styles. These advancements make it simple to develop one-of-a-kind pieces without the high costs of conventional display printing. In addition, on the internet layout systems encourage you to visualize your concepts prior to printing.
Picking the Right Ink for Your Layouts
Just how do you select the ideal ink for your display printing styles? Begin by taking into consideration the kind of fabric you're working with. For cotton, water-based inks are optimal as they take in well and give a soft feeling. Plastisol inks offer durability and lively shades. if you're printing on synthetic materials.
Next, consider the surface you want. Matte inks offer a subtle appearance, while shiny inks can add a striking luster. If more you're aiming for eco-friendliness, go with soy-based or water-based inks, which are much better for the atmosphere.
Do not forget color blending; some inks can be blended to develop special tones. Examine your inks on example materials to verify compatibility and look before beginning your primary task. Eventually, the right ink can make a significant distinction in the high quality and durability of your styles, so select intelligently!
Tips for Creating Stunning Tee Shirt Designs
Creating magnificent t-shirt styles begins with a clear principle that resonates with your target market. Bear in mind, simplicity often functions finest; chaotic designs can puzzle visitors.
Incorporate typography that shows the personality of your brand-- select typefaces that are legible yet trendy, and blend them wisely. Take notice of positioning; the design must flow naturally with the tee's shape.
Try out various designs, such as contemporary or classic, to discover what fits best. Do not avoid utilizing adverse area properly; it can create a striking visual effect.
Finally, get comments! Share your designs with friends or possible clients to assess their reactions (t-shirt printing). Their understandings can direct you in refining your job, ensuring your last style is not just spectacular however likewise market-ready
Repairing Common Screen Printing Obstacles
When you experience obstacles in screen printing, determining the root cause can make all the difference. If you notice incomplete prints, inspect your screen for appropriate stress and confirm your emulsion is totally cured. For smearing or fuzzy photos, it might be due see this here to inappropriate ink viscosity or inadequate healing time; adjust your ink or remedy settings accordingly.
If you're managing shade inequalities, confirm your ink blending ratios and confirm your displays are complimentary and clean of residue.
Last but not least, if you're experiencing training or peeling, think about the sort of material you're utilizing and the warm used throughout healing; different materials call for details inks and temperature levels. By resolving these usual problems systematically, you'll enhance your outcomes and enhance your self-confidence in display printing. Keep trying out, and do not be reluctant to connect to fellow printers for suggestions and suggestions.
Frequently Asked Questions
Can I Evaluate Print on Material Aside From T-Shirts?
Definitely, you can screen print on different textiles besides tee shirts! Think about items like tote, hoodies, and even table linens. Just ensure you're using the appropriate ink and tools appropriate for the fabric type.
Just how Do I Tidy and Maintain My Screen Printing Devices?
To clean and preserve your screen printing tools, consistently clean displays with water and appropriate cleansers, check squeegees for damages, and shop every little thing in a completely dry, dust-free atmosphere to prolong its life expectancy and ensure high quality prints.
What Is the Average Price of Starting a Display Printing Service?
Beginning a screen printing business typically costs between $2,000 and $10,000. You'll require devices, materials, and a work space. It's necessary to spending plan intelligently and strategy for extra expenditures as your organization expands.
Is Display Printing Eco-friendly?
If you select sustainable materials and eco-conscious inks,Screen printing can be ecologically pleasant. By adopting best techniques and decreasing waste, you can lower your influence while creating dynamic, top notch prints that attract mindful customers.
How Can I Promote My Personalized Tee Shirt Layouts Efficiently?
To advertise your custom tee shirt designs effectively, leverage social media sites systems, collaborate with influencers, run targeted advertisements, and engage your target market with contests or giveaways. Regular branding and quality visuals will draw in more clients.
Discovering the Art of Display Printing: A Comprehensive Guide to T-Shirt Printing Strategies
Begin with a sturdy display printing framework, which holds the mesh that moves ink onto Read More Here your fabric. By spending in the best inks and solutions, you'll raise your display printing video game significantly.
With advancements in ink high quality, you can anticipate sturdiness and washability that measures up to screen printing.Exactly how do you pick the appropriate ink for your screen printing layouts?
Report this page